Biotech & Medical
Biotech & Medical
Biotech & Medical
Design Innovation has designed various fixtures, devices, and labware for the biotech, medical, and health & wellness industries. We've worked with tech startups, established companies, hospital labs, and university labs.
Design Innovation has designed various fixtures, devices, and labware for the biotech, medical, and health & wellness industries. We've worked with tech startups, established companies, hospital labs, and university labs.
Design Innovation has designed various fixtures, devices, and labware for the biotech, medical, and health & wellness industries. We've worked with tech startups, established companies, hospital labs, and university labs.
Test Fixture for Laparoscopic Scissors
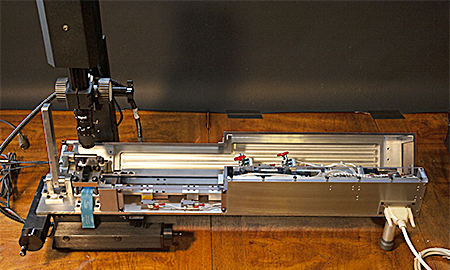
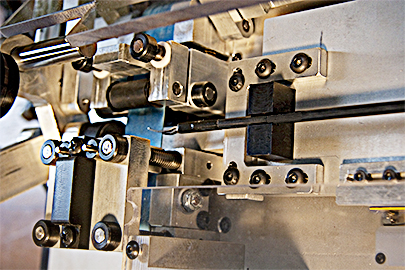
A surgical device manufacturer needed to be able to test several different styles of laparoscopic scissors, each having different cutting characteristics and needing different ranges of cutting forces measured for pass/fail testing.
We worked with the manufacturer to develop this test fixture, which allowed each style of scissor to be tested to their specified parameters against a uniform material to be test cut. A digital microscope camera was also integrated into the test fixture to provide a detailed image of each test cut. The fixture included a safety interlock enabled polycarbonate cover, so that no movement of any parts could happen unless the cover was completely closed, and all internal workings could be observed.
The fixture also included a control panel with a selector dial for scissor type, status indicators, a manual/automatic switch, and a pass/fail indicator.
A material feed and tensioning mechanism provided a fresh and uniform test sample for each cut.
See more information about this project at Devices & Fixtures.
A surgical device manufacturer needed to be able to test several different styles of laparoscopic scissors, each having different cutting characteristics and needing different ranges of cutting forces measured for pass/fail testing.
We worked with the manufacturer to develop this test fixture, which allowed each style of scissor to be tested to their specified parameters against a uniform material to be test cut. A digital microscope camera was also integrated into the test fixture to provide a detailed image of each test cut. The fixture included a safety interlock enabled polycarbonate cover, so that no movement of any parts could happen unless the cover was completely closed, and all internal workings could be observed.
The fixture also included a control panel with a selector dial for scissor type, status indicators, a manual/automatic switch, and a pass/fail indicator.
A material feed and tensioning mechanism provided a fresh and uniform test sample for each cut.
See more information about this project at Devices & Fixtures.
A surgical device manufacturer needed to be able to test several different styles of laparoscopic scissors, each having different cutting characteristics and needing different ranges of cutting forces measured for pass/fail testing.
We worked with the manufacturer to develop this test fixture, which allowed each style of scissor to be tested to their specified parameters against a uniform material to be test cut. A digital microscope camera was also integrated into the test fixture to provide a detailed image of each test cut. The fixture included a safety interlock enabled polycarbonate cover, so that no movement of any parts could happen unless the cover was completely closed, and all internal workings could be observed.
The fixture also included a control panel with a selector dial for scissor type, status indicators, a manual/automatic switch, and a pass/fail indicator.
A material feed and tensioning mechanism provided a fresh and uniform test sample for each cut.
See more information about this project at Devices & Fixtures.
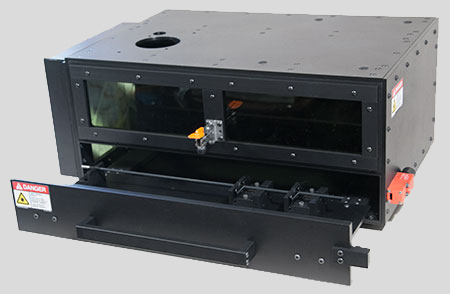
Laser Etching Fixture for Surgical Devices
A surgical device manufacturer needed to be able to laser mark the handles and shafts on a group of laparoscopic surgical tools. Several of this fixture were designed and built to enable a marking laser to be fastened to the top surface, and for a safety interlock switch to be wired into the laser controller.
A sliding drawer connected to the interlock provided access to a mounting platform, onto which holding nests for the handles and shafts were attached. The slides and stops were precisely located for repeatable positioning of the items to be marked. A side-mounted fan with an interchangeable filter removed fumes and particulates from the marking chamber.
See more information about this project at Devices & Fixtures.
Laser Etching Fixture for Surgical Devices
A surgical device manufacturer needed to be able to laser mark the handles and shafts on a group of laparoscopic surgical tools. Several of this fixture were designed and built to enable a marking laser to be fastened to the top surface, and for a safety interlock switch to be wired into the laser controller.
A sliding drawer connected to the interlock provided access to a mounting platform, onto which holding nests for the handles and shafts were attached. The slides and stops were precisely located for repeatable positioning of the items to be marked. A side-mounted fan with an interchangeable filter removed fumes and particulates from the marking chamber.
See more information about this project at Devices & Fixtures.
Laser Etching Fixture for Surgical Devices
A surgical device manufacturer needed to be able to laser mark the handles and shafts on a group of laparoscopic surgical tools. Several of this fixture were designed and built to enable a marking laser to be fastened to the top surface, and for a safety interlock switch to be wired into the laser controller.
A sliding drawer connected to the interlock provided access to a mounting platform, onto which holding nests for the handles and shafts were attached. The slides and stops were precisely located for repeatable positioning of the items to be marked. A side-mounted fan with an interchangeable filter removed fumes and particulates from the marking chamber.
See more information about this project at Devices & Fixtures.
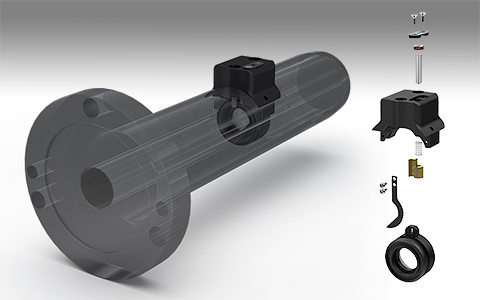
Dental Laser Shutter Retrofit Prototype
An existing dental laser shutter wasn't providing a sufficient range of adjustment. It was clear to the client from the beginning of the project that the adjustment mechanism would have to increase in size. We worked with them to find an acceptable direction in which to enlarge the mechanism.
We also worked with the goal of changing their existing design and the existing parts as little as possible. We were able to provide the required adjustment range, and with acceptable changes to the parts and mechanism.
See more information about this project at Rapid Prototyping.
Dental Laser Shutter Retrofit Prototype
An existing dental laser shutter wasn't providing a sufficient range of adjustment. It was clear to the client from the beginning of the project that the adjustment mechanism would have to increase in size. We worked with them to find an acceptable direction in which to enlarge the mechanism.
We also worked with the goal of changing their existing design and the existing parts as little as possible. We were able to provide the required adjustment range, and with acceptable changes to the parts and mechanism.
See more information about this project at Rapid Prototyping.
Dental Laser Shutter Retrofit Prototype
An existing dental laser shutter wasn't providing a sufficient range of adjustment. It was clear to the client from the beginning of the project that the adjustment mechanism would have to increase in size. We worked with them to find an acceptable direction in which to enlarge the mechanism.
We also worked with the goal of changing their existing design and the existing parts as little as possible. We were able to provide the required adjustment range, and with acceptable changes to the parts and mechanism.
See more information about this project at Rapid Prototyping.
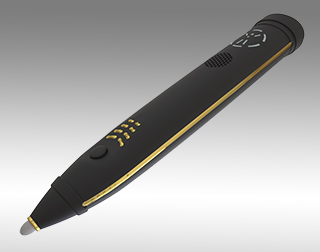
Handheld Device for Use in the Health & Wellness Industry
This proof-of-concept prototype device uses multiple electrodes in order to measure specific physical parameters. The enclosure is intended to be sealed against liquids, has a moisture-proof pressure vent, and contains a wireless rechargeable battery.
The user interface includes a sealed pushbutton, multiple LEDs forming a primary status indicator, a sealed speaker for audio feedback, and an internal haptic output device for additional user feedback.
See more information about this project at Product Design and Rapid Prototyping.
Handheld Device for Use in the Health & Wellness Industry
This proof-of-concept prototype device uses multiple electrodes in order to measure specific physical parameters. The enclosure is intended to be sealed against liquids, has a moisture-proof pressure vent, and contains a wireless rechargeable battery.
The user interface includes a sealed pushbutton, multiple LEDs forming a primary status indicator, a sealed speaker for audio feedback, and an internal haptic output device for additional user feedback.
See more information about this project at Product Design and Rapid Prototyping.
Handheld Device for Use in the Health & Wellness Industry
This proof-of-concept prototype device uses multiple electrodes in order to measure specific physical parameters. The enclosure is intended to be sealed against liquids, has a moisture-proof pressure vent, and contains a wireless rechargeable battery.
The user interface includes a sealed pushbutton, multiple LEDs forming a primary status indicator, a sealed speaker for audio feedback, and an internal haptic output device for additional user feedback.
See more information about this project at Product Design and Rapid Prototyping.
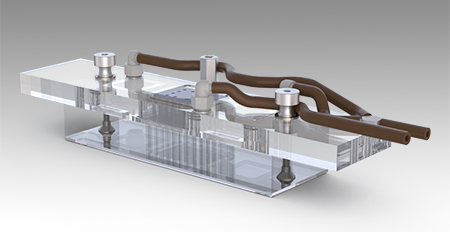
Slide Holding and Positioning Fixture
A university lab needed a custom transparent fixture for attaching to a glass slide and a cast clear rubber block with thru channels to access features on the slide. The fixture needed to also act as a manifold attached to a two-channel vacuum apparatus, with the entire fixture assembly mounted on a micropositioning stage. Mechanical fasteners were also included to provide positive locking once the vacuum had pulled the slide into full contact with the block.
See more information about this project at Devices & Fixtures.
Slide Holding and Positioning Fixture
A university lab needed a custom transparent fixture for attaching to a glass slide and a cast clear rubber block with thru channels to access features on the slide. The fixture needed to also act as a manifold attached to a two-channel vacuum apparatus, with the entire fixture assembly mounted on a micropositioning stage. Mechanical fasteners were also included to provide positive locking once the vacuum had pulled the slide into full contact with the block.
See more information about this project at Devices & Fixtures.
Slide Holding and Positioning Fixture
A university lab needed a custom transparent fixture for attaching to a glass slide and a cast clear rubber block with thru channels to access features on the slide. The fixture needed to also act as a manifold attached to a two-channel vacuum apparatus, with the entire fixture assembly mounted on a micropositioning stage. Mechanical fasteners were also included to provide positive locking once the vacuum had pulled the slide into full contact with the block.
See more information about this project at Devices & Fixtures.
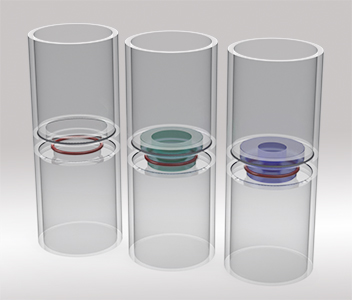
Polycarbonate Medical Labware
These polycarbonate containers were designed and fabricated for a research group at a local hospital, and are used for holding cell culture vessels in a medical lab. The containers were fabricated from polycarbonate tubes and rods with silicone rubber O-rings to provide liquid-tight seals for the cell culture vessels and adapter pieces. (The adapter pieces are shown in color for visual contrast.) Polycarbonate was chosen for cell culture compatibility, transparency, ability to withstand autoclaving, and ease of machining. The first units built were immediately usable after initial sterilization.
Polycarbonate Medical Labware
These polycarbonate containers were designed and fabricated for a research group at a local hospital, and are used for holding cell culture vessels in a medical lab. The containers were fabricated from polycarbonate tubes and rods with silicone rubber O-rings to provide liquid-tight seals for the cell culture vessels and adapter pieces. (The adapter pieces are shown in color for visual contrast.) Polycarbonate was chosen for cell culture compatibility, transparency, ability to withstand autoclaving, and ease of machining. The first units built were immediately usable after initial sterilization.
Polycarbonate Medical Labware
These polycarbonate containers were designed and fabricated for a research group at a local hospital, and are used for holding cell culture vessels in a medical lab. The containers were fabricated from polycarbonate tubes and rods with silicone rubber O-rings to provide liquid-tight seals for the cell culture vessels and adapter pieces. (The adapter pieces are shown in color for visual contrast.) Polycarbonate was chosen for cell culture compatibility, transparency, ability to withstand autoclaving, and ease of machining. The first units built were immediately usable after initial sterilization.
design@design-innovation.org 781-883-5666
design@design-innovation.org 781-883-5666
design@design-innovation.org
781-883-5666